The Impact of Laser Cleaning Devices on Metal Fabrication
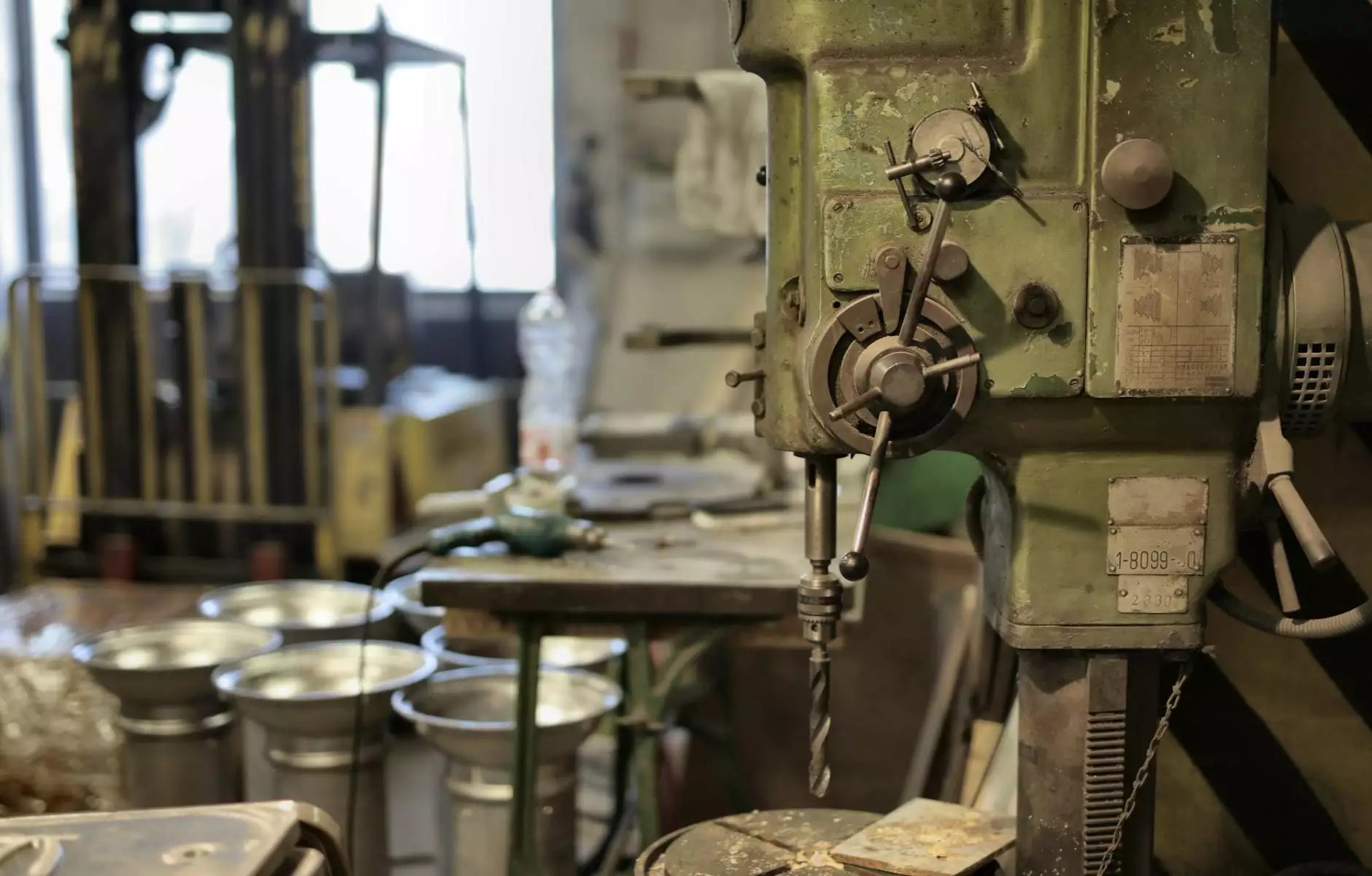
In the realm of Metal Fabricators, innovation has always been a driving force, constantly pushing the boundaries of what is possible in the fabrication industry. One such groundbreaking technological advancement that has revolutionized metal fabrication operations is the laser cleaning device.
Understanding Laser Cleaning Devices
Laser cleaning devices utilize the power of laser technology to efficiently and effectively remove contaminants, rust, paint, oxides, and other unwanted substances from various metal surfaces. This process is achieved through the precise and targeted application of laser beams, which vaporize or ablate the surface impurities without damaging the underlying material.
The Benefits of Laser Cleaning Devices
One of the key advantages of using laser cleaning devices in metal fabrication is their non-contact and non-abrasive nature. Unlike traditional cleaning methods that may involve harsh chemicals or abrasive techniques, laser cleaning offers a clean and environmentally friendly solution that eliminates the need for hazardous materials and minimizes waste.
Enhanced Precision and Control
Laser cleaning devices provide operators with unparalleled precision and control over the cleaning process, allowing them to target specific areas on a metal surface with utmost accuracy. This level of control ensures that only the desired contaminants are removed, leaving the rest of the surface untouched.
Increased Efficiency and Cost Savings
By streamlining the cleaning process and minimizing the need for manual labor, laser cleaning devices help Metal Fabricators increase their efficiency and productivity. The reduced downtime and labor costs translate into significant cost savings over time, making laser cleaning a cost-effective solution for businesses.
Applications of Laser Cleaning Devices
The versatility of laser cleaning devices makes them suitable for a wide range of applications within the Metal Fabricators industry. From removing weld residues and coatings to preparing surfaces for bonding or painting, laser cleaning devices play a crucial role in enhancing the quality and durability of metal components.
Surface Preparation
One of the primary applications of laser cleaning devices is surface preparation, where they are used to clean and pre-treat metal surfaces before welding, painting, or coating. By removing contaminants and oxides, laser cleaning ensures proper adhesion and improves the overall quality of surface treatments.
Rust and Oxide Removal
Rust and oxide formation on metal surfaces can compromise their integrity and aesthetics. Laser cleaning devices offer a quick and efficient solution for removing rust and oxides, restoring the metal to its original state and prolonging its lifespan.
Conclusion
In conclusion, laser cleaning devices have emerged as a game-changer in the Metal Fabricators industry, offering a cutting-edge solution for efficient and environmentally friendly metal cleaning. As businesses strive to enhance their operations and stay ahead of the competition, integrating laser cleaning devices into their fabrication processes can provide a competitive edge and contribute to the overall success of their operations.
Visit DP Laser today to explore how laser cleaning devices can transform your metal fabrication processes and elevate the quality of your products.