Understanding Die Casting Production: A Comprehensive Guide
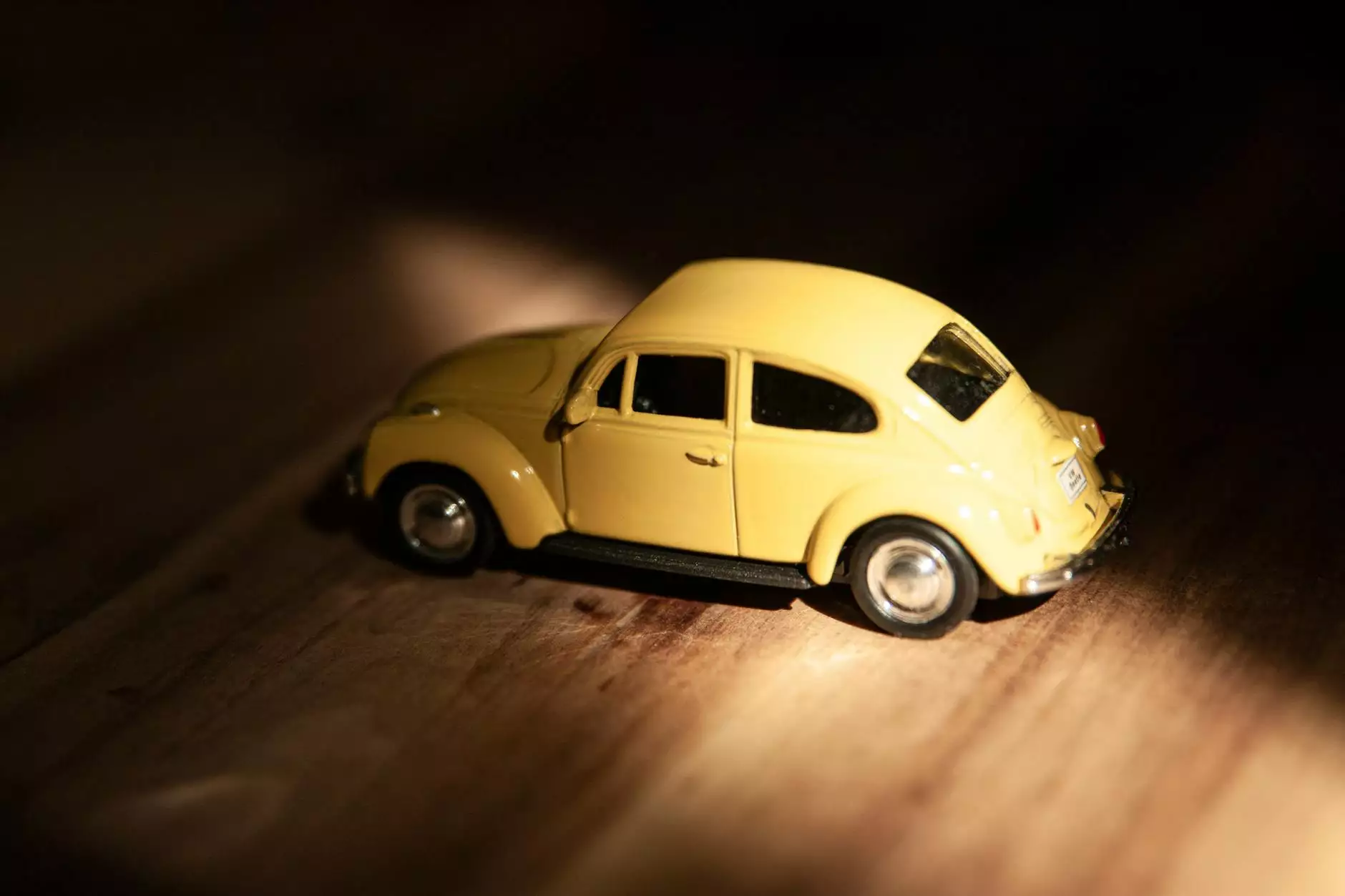
Die casting production is a specific manufacturing process used in the metal fabrication industry. It is characterized by its ability to create complex shapes and high-precision components. This article seeks to provide you with an in-depth understanding of the die casting process, its benefits, and its vast applications across various industries.
What is Die Casting?
Die casting is a metal casting process that involves forcing molten metal under high pressure into a mold cavity. The mold is usually made of high-quality steel with an intricate design to produce the desired shape of the final product. The die casting process is widely used for producing metal parts with high dimensional accuracy and smooth surface finishes.
The Die Casting Process
The die casting production process can be divided into several crucial steps that ensure the final product meets the required specifications. Here's a breakdown of these steps:
1. Mold Preparation
The first step in die casting production is the preparation of the mold. The molds are designed and manufactured according to the specifications of the part to be produced. This involves:
- Designing the Mold: Using CAD software to create a 3D model.
- Machining the Mold: Precision machining is performed to create the mold cavity.
- Testing the Mold: Ensuring the mold can withstand high pressure and heat.
2. Choosing the Right Metal Alloy
The selection of metal alloys is critical in die casting production. Common materials include:
- Zinc: Known for its low melting point and excellent fluidity, making it ideal for intricate designs.
- Aluminum: Lightweight and strong, aluminum is popular in automotive and aerospace industries.
- Magnesium: Light and has good mechanical properties, suitable for various applications.
3. Melting the Metal
The chosen metal alloy is heated until it reaches a molten state. This requires precise temperature control to ensure optimal flow during the casting process.
4. Injecting the Molten Metal
Once the metal is molten, it is injected into the mold at high pressure. The high pressure ensures that the metal fills the mold completely, preventing defects.
5. Cooling and Solidification
After the molten metal is injected, it is allowed to cool and solidify within the mold. The cooling time varies depending on the metal and the thickness of the part.
6. Ejecting the Casting
Once the metal has cooled and solidified, the mold opens, and the finished product is ejected. This step requires precision to avoid damaging the casting.
Benefits of Die Casting Production
Die casting production offers several advantages that make it a preferred choice in metal fabrication:
1. High Precision and Dimensional Accuracy
One of the key benefits of die casting is its ability to produce parts with tight tolerances. This is essential in industries where precision is critical, such as aerospace and automotive.
2. Excellent Surface Finish
Die cast parts often require minimal finishing, as the molds are designed to produce smooth surfaces. This reduces secondary operations, saving time and costs.
3. Complex Shapes and Designs
The die casting process allows manufacturers to create complex shapes that may be challenging or impossible to achieve with other manufacturing methods. This capability is essential in modern product design.
4. High Production Rates
Because the die casting process is highly automated, it allows for high production rates. Multiple parts can be produced in a short amount of time, making it ideal for mass production.
5. Material Efficiency
Die casting minimizes waste, as the process allows for precise control of the metal being used. Scrap rates are low compared to other manufacturing processes.
Applications of Die Casting
Die casting production is utilized in various industries due to its versatility. Here are some common applications:
1. Automotive Industry
The automotive sector is one of the largest consumers of die-cast parts. Components such as engine blocks, transmission cases, and other intricate parts are often manufactured through die casting.
2. Aerospace Industry
In aerospace, where weight and durability are paramount, die cast components like brackets and housings are essential for ensuring structural integrity and performance.
3. Electronics
Many electronic devices require housings and structural parts made from die-cast aluminum or zinc due to their excellent thermal and electrical conductivity.
4. Consumer Products
Household goods such as kitchen appliances and tools often feature die-cast parts that enhance their durability and aesthetic appeal.
5. Industrial Equipment
Die casting is also prevalent in industrial settings, where equipment such as hydraulic housings and motor components are manufactured.
The Future of Die Casting Production
As technology advances, die casting production is set to become even more efficient. Innovations such as:
- 3D Printing of Molds: Reducing lead times and costs.
- Improved Alloy Technologies: Enhancing properties and applications of die cast parts.
- Automation and Industry 4.0: Streamlining processes and improving quality control through the use of AI and IoT.
Conclusion
In summary, die casting production is a cornerstone of modern manufacturing. With its unmatched precision, efficiency, and versatility, it plays a vital role in many industries. As technology evolves, die casting will continue to adapt and thrive, offering innovative solutions for complex manufacturing challenges. Understanding this process is fundamental for anyone involved in metal fabrication or looking to leverage its benefits for their business.
For more insights and information about die casting and other metal fabrication processes, consider visiting DeepMould.net, your resource for high-quality metal fabrication solutions.